Ever since Burger King promised to indulge our every kinky whim if only we'd please buy their baps, consumer expectations have soared. These days, everyone wants to "have it their way" - and, predictably, the trend for bespoke has found fertile ground among the fettlers and fetishists of the cycling world. For some cyclists 'factory-built' is fast becoming the new f-word, and nowhere is this more true than in the case of wheels.
Bespoke wheelbuilders are nothing new, and some of the old guard have moved with the times and taken their business online - I'm still running a set of Ambrosio Excellight built by Harry Rowland a couple of years ago.
But lately a clutch of new and predominantly online wheel building companies has emerged. These companies offer a dizzying array of hub, rim and spoke combos allowing customers to tweak every detail to achieve their dream package of weight, durability, aerodynamics, aesthetics and budget.
I have a tendency to imagine that all online businesses are operated by robots from a vague and ethereal cloudland, rather than somewhere real. So I was amazed to discover that one of these purveyors of hand built wheels, Strada Wheels, is located just down the road from me in Sussex. It seemed too good a coincidence to pass up - I got in touch and asked if I could pop over for a chat. A prompt reply came back from founder Jonathan Day, welcoming me over. Just one thing: "We're a working workshop," he cautions, "so you take us as you find us!"
It turns out that finding Strada's office in the first place is the hard part. After several bewildered laps of an industrial estate a few miles west along the coast from Brighton, I finally swallow my pride and phone for directions.
Jonathan is grinning as I finally peer around the door of Strada HQ. "You found us!"
Strada Wheels is Jonathan's brainchild. A keen cyclist, he founded Strada Wheels in 2011 after giving up his previous job as a photographer. He hasn't given up on photography entirely though. On the day of my visit, he's set up a lightbox on a work bench and is busy photographing an array of gleaming high-end wheel components.
"We're re-launching the website," Jonathan explains between shots, "so I'm taking new photos of our stock for the image library."
He removes a pristine Tune hub from the lightbox and puts it carefully back in its box before rooting around on the shelves. The object he produces next is far from pristine. He shows me a grimy, battered hub and freewheel that looks like it's been used as a chewtoy by a bear.
"We've just got this freehub back from our supported rider, Josh Lawless," he explains. "He's living and racing over in Brittany. The standard is a different level over there. We just help him out with new wheels. And every so often he sends back bits like this, completely shagged. This gives us vital feedback as to how components handle extreme conditions and workload."
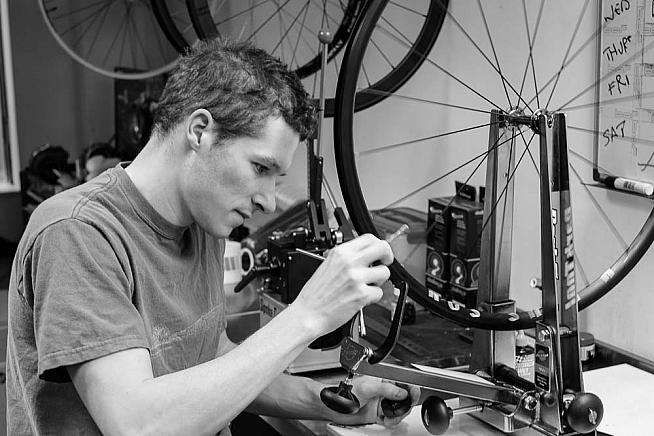
I'm impressed by the fact that Strada are helping out local prospects, and also by the atmosphere in the small premises, which manages the trick of appearing both busy and laid back at the same time. The three members of staff who are here today - Jonathan, wheelbuilder Ben and apprentice Mike - are happy to take time to chat as they go about their work.
I ask Jonathan what the idea was behind Strada Wheels, the founding philosophy.
"Wheels hand built in the UK, by people who ride bikes," he replies. "We're all cyclists here.
"The idea for Strada came from that passion for cycling, and it's taken on a life of its own really as a small business grows. We've really benefitted from the popularity of cycling as people look to trade up. Wheels are one of the best upgrades you can make."
The Strada team are clearly huge cycling enthusiasts. From the cycling prints on the wall to the Hope mini disc brake coasters on Jon's desk, it's apparent that this is more than just a job to them. Ben is an avid roadie - "a mile monster" in Jonathan's words - while I discover that the Surly touring bike leaning in the corner belongs to Mike, who is about to embark on a tour of Southeast Asia.
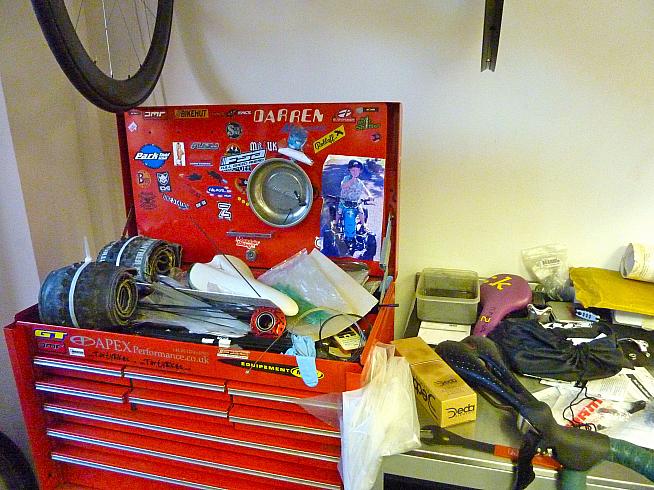
A fourth member of the team, Strada's senior wheelbuilder Darren, is off duty today. "A pity he's not here," Jonathan says, "he'd talk your ear off about wheels."
Jonathan explains how the team operates. He takes care of the business side of things, running the website and processing orders, while Ben assists in admin while learning the finer points of the art of wheelbuilding.
When an order comes in, Ben or Mike will do the initial build of the wheel, lacing the hub to the rim in the appropriate spoke pattern. Ben will then work on the initial tensioning and stressing, before passing it on to Darren for the final truing on his P+K Lie truing stand.
"I get them true to about 0.5mm," Ben explains. "Then Darren finishes it on the bench over there. He works to 0.05mm, so...yeah, pretty tight tolerances."
"Darren has OCD when it comes to wheels," Jonathan adds, "which is actually a really good thing for a wheelbuilder to have."
I can see why that might be: threading spokes, tweaking nipples in minute increments and then dishing and truing to hundredths of a millimetre, wheelbuilding seems an exacting task. Attention to detail, not to mention patience, must be a prerequisite.
As we talk Darren's name crops up regularly in conversation. It reminds me of Flann O'Brien's surreal novel The Third Policeman - a must-read for cycling fans, incidentally - where the elusive Sergeant Fox is referred to in absentia by his bicycle-obsessed colleagues.
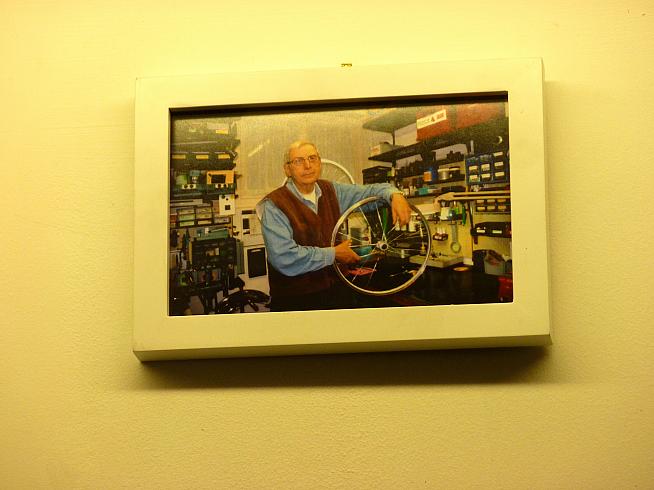
At one point, spotting a framed photograph of a stern-looking chap pinned to the wall above the workbench, I ask if that's Darren. Ben bursts into a laugh, then looks sheepish. "No, that's...well, it's a bit embarrassing really, it's kind of a joke. That's Gerd Schraner..."
When I look at him blankly, he shows me a well-worn copy of a book sitting on Mike's desk. I check the title page: 'The Art of Wheelbuilding.'
"Gerd is this legendary old wheel builder," Ben explains, "he wrote this book on wheelbuilding. It's great as a reference."
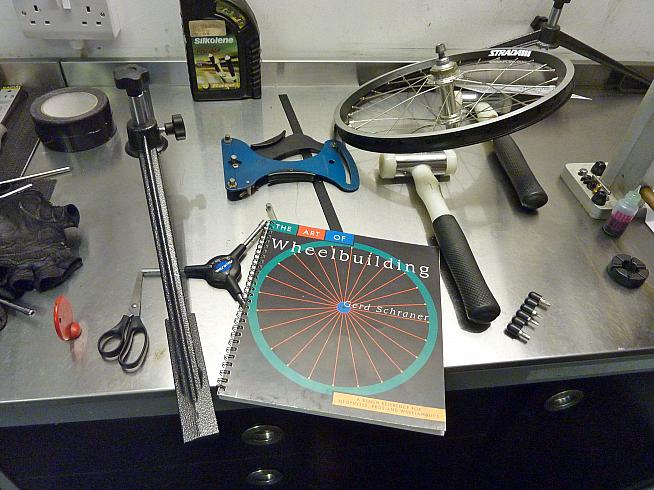
While the guys get on with their work, I have a little nosy around the office-cum-workshop. The large room is divided into two zones, with one corner dedicated to office equipment - desks, and a couple of computers - while the other end of the room has a long workbench with perhaps a dozen completed wheels hanging from a rail above.
I spot the distinctive dome-capped hub of a PowerTap wheel in the rack, and Ben lifts it down for me to have a look.
"We've rebuilt this wheel for a customer using a new rim on his PowerTap hub," he explains.
"To be honest the PowerTap hubs don't build up very well. It's because the large flange diameter is tricky for spoke tensions. But this wheel is a lot stronger now than when he sent it to us. He won't have any problems."
There are a few other curiosities among the finished wheels, including a pair of teeny 16" wheels, the sort you'd find on a Brompton. But Strada's best sellers are high-quality 700c road and racing builds - the H Plus Son Archetype rim is especially popular.
When I ask what their own favourite wheel is, Ben shows me a beautiful carbon mid-section rim. "This is our new wheel, the Rail 52mm carbon clincher" he tells me. "We've just got a deal to import these from the US, as the UK distributor. I've been riding it and they're so fast, just amazing, it's a great rim."
I ask if they build wheels for customers who already have the parts. "Not usually," Jonathan says, "unfortunately it just wouldn't be worth it for us, economically. But if someone came to us with NOS rims or a classic hub they wanted building up, we'll do one-off jobs like that."
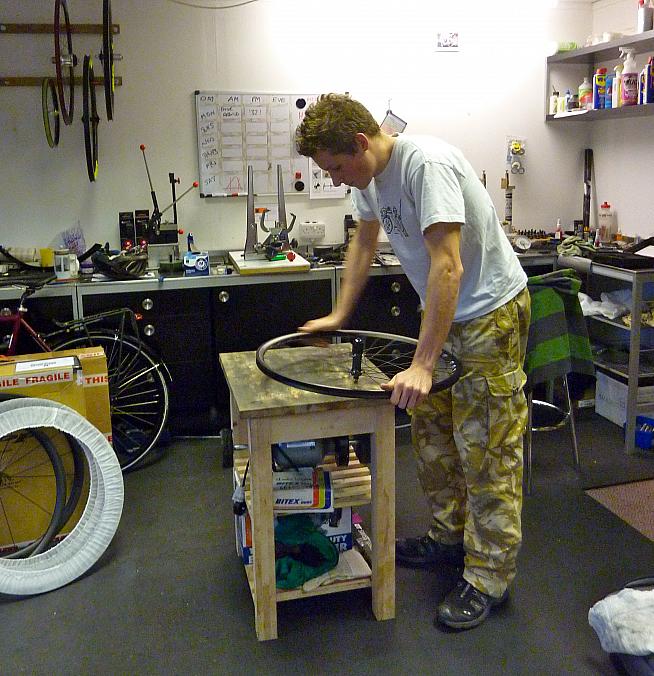
Putting the wheel back, Ben returns to his current build. He takes the wheel he's just finished lacing up over to a side table and leans his full weight on the rim, pressing down with both hands to destress the spokes. I ask him how often he does this during a build.
"Six to eight flexes per wheel on both sides, then check tension and true... I'll do that six to 10 times typically per wheel," he replies.
"It takes time to build a wheel properly. At the moment a set takes me about four hours. I could build one in half an hour, but it just wouldn't be anywhere near as good."
It's been a fascinating glimpse into the world of wheels, but I'm conscious that the guys have work to do and I've taken up enough of their time. Besides, I want to be sure of finding my way out of the labyrinthine industrial estate before darkness falls.
As I'm leaving, I mention that if any of the guys ever feel like testing their wheels on a sportive for us we'd welcome a report. Ben's eyes light up. "Actually, there is this one ride I'd like to do...it's 222 miles in 14 hours." He tells me about the Welsh Coast to Coast Challenge.
"I'm doing La Marmotte the week before," he adds, giving the wheel a final flex, "so that will be good preparation."
Now that's dedication to your job.
If you're after a custom wheelbuild, and want to know your wheels are in the hands of someone who lives and breathes cycling, pay a visit to Strada. With a "free true for life" policy, you can rest easy that you're investing in a quality product built with true care.
And it's not just us saying that; we'll leave the final word to the guru himself, Gerd Schraner:
"The final decision between buying 'handmade' or ready-made wheels lies solely with the user. Should he decide on the former, then the value of his or her bike will be enhanced by these worry and problem-free jewels."
0 Comments